Chemplast Sanmar turns 50: Sankar bats for measured protectionism
Chemplast Sanmar Limited is all set to launch its golden jubilee celebrations on May 4, 2017.
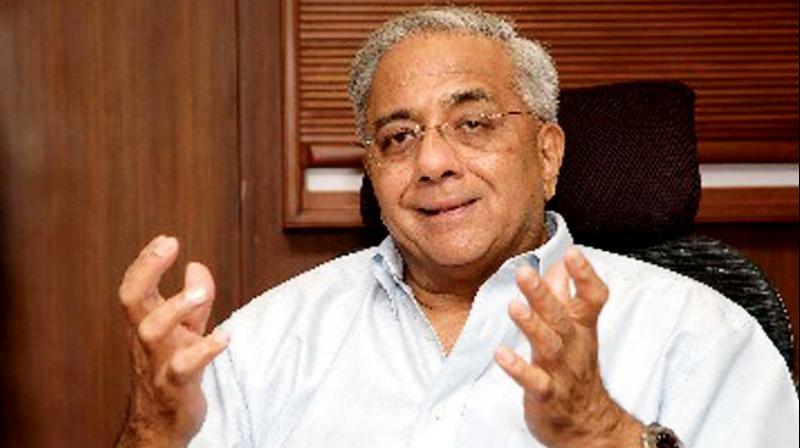
New industrial enterprises widen space-time horizons as much as they as they incubate in a favourable, yet dynamically changing milieu. The decade since the late 1950s’ in Tamil Nadu, widely acknowledged as the ‘golden era of industrialisation’ had laid the foundations for long-term growth of this Southern state. Piloting Chemplast Sanmar, the flagship company of the Chennai-based Sanmar Group, a US$ 1.5 billion industrial conglomerate, involved in Chemicals, Specialty Chemicals, Engineering, Steel Castings and Shipping, N Sankar, with a chemical engineering background and who is also Chairman of the group, will be completing 50 years with its core company, as Chemplast Sanmar Limited is all set to launch its golden jubilee celebrations on May 4, 2017.
Looking back at 50 years of Chemplast Sanmar, now one of the two leading PVC resins producers in the country, Sankar in an exhaustive interview to the ‘Deccan Chronicle’, spoke on a wide range of issues: Excerpts from the interview he gave to SHRUTI SURESH AND M.R. VENKATESH
Q. How did you foray into PVC and the building blocks of a 50-year-old enterprise?
Sankar: I can’t claim credit for starting the business, but I am very closely bound to the company. With the golden jubilee of Chemplast Sanmar, I am also completing 50 years with the company. The first day I saw Chemplast was on May 4, 1967, when I first visited it on its inauguration day in Mettur where I happened to be that day. Officially, I joined Chemplast on May 22, 1967, after I had returned from the U.S. Chemplast started as a very unique idea those days. It was an outcome of R Venkatraman’s (who as State Industries Minister in K Kamraj’s cabinet had laid the foundation stone in 1965), thrust. The concept was to use two by-products that were being wasted and put value addition to bring a state-of-the-art product. One was chlorine at Mettur Chemical, a by-product and poisonous gas that had to be fixed and another was the noxious by-product of sugar mills, molasses coming out and spreading a stink around. The unique process we undertook involved making alcohol from molasses by fermenting and distilling it, from alcohol make ethylene and use that ethylene to combine it with chlorine to make PVC, a state-of-the-art polymer at that time.
It was a big deal to get a foreign collaboration those days and we managed to set up a joint venture, that too with a company like BF Goodrich, USA, a world leader in tyres and rubberized plastics. They came to work with us in India and invested in the company. The promoters of the company included my father (Iate K S Narayanan), T.S. Narayanaswamy (late visionary industrialist and founder of India Cements), Loganatha Mudaliar and Palani, ...they started the joint venture on May 4, 1967. This was the first big project that was commissioned after the DMK came to power in Tamil Nadu. Then Chief Minister, C.N. Annadurai, his cabinet colleague, V R Nedunchezhiyan were there, and Ashok Mehta, then Union Petroleum Minister was there. We started with 6,000 tonnes of PVC and today we are at over 3.50 lakh tonnes of PVC. It has grown, made a lot of progress, right from when Chemplast started...we have had very good and very very difficult periods, pretty standard for a commodity business.
Q. The issues and challenges you encountered in your growth story?
A: When we started manufacturing PVC from ethylene and chlorine, with ethylene got from alcohol, it was an unusual process. We had set up a pilot plant in Boston and then here, when it was started, we ran into one big problem in two months. One of the Heat Exchangers corroded completely and the plant had to be shut down...those days you had to virtually import everything as you couldn’t get chemical equipment locally. We looked around and BHEL, Tiruchy, did a special help to us; my father met V Krishnamurthy, who was then GM at the Tiruchy plant. They took it on as a challenge, as a special case, and in two months they fabricated a Heat Exchanger and gave it to us. This was one problem. ...There was another major problem after the foundation stone was laid. In 1965 when we started, we had a foreign exchange loan as we had to import most of the stuff. But in 1966, the Rupee was devalued and our project cost suddenly went up 50 per cent to 60 per cent!
The third problem related to PVC itself being in a fledgling phase then. . Only two manufacturers of PVC then, DCM (Delhi Cloth Mills) and Calico Mills. Both added capacity and the prices collapsed by 50 per cent... So, the first three to four years was very difficult for us, there were labour problems too. By 1972, things turned around. Then prohibition was introduced (in Tamil Nadu) in 1977, while the import duty on PVC dropped to 40 per cent even in the 1980s’, much before economic liberalisation. Thus, from 1967 when we started, till 1977 we were keeping things going. Then, in 1977, (when Sankar was by then at the helm), we launched a number of things, started first with capacity expansion to 20,000 tonnes of PVC, set up a distillery in Krishnagiri to make our own alcohol as it was getting diverted (for drinking); then in the mid-1980s, we acquired Mettur Chemicals to ensure we had a source of chlorine...then acquired Aravind distillery to set up our second distillery for alcohol... we ensured all the raw materials got integrated by backward integration. And another big contribution was we brought in PVC pipes into the country. PVC pipes were not known then and people were using GI pipes or AC pipes. ...
Then we realized that we were constrained by the fact that we were land-locked in Mettur...As by 1980s’, we started importing our raw materials and first we started with Ethylene dichloride, an important raw material. By late 1990s’ and early 2000, we realized that to be in the chemicals business, we had to be on the coast... In that phase, we set up two new plants in Karaikal and Cuddalore.
In Karaikal, we acquired Kothari Sugars and caustic soda plant and set up an Ethylene dichloride (EDC) manufacturing plant based on imported Ethylene. By that time, local alcohol had completely dried up... So we made EDC at Karaikal and shifted it to Mettur. We had set up a marine terminal facility at Karaikal for that. The second marine terminal was set up at Cuddalore, when we expanded our PVC capacity (in 2007-08). But the day work on the Karaikal maritime terminal was to be started the Tsunami (December 26, 2004) struck! The canteen contractor had just set up his kitchen and he was killed! So we had to redesign the Kariakal terminal because the marine contour had changed. In Cuddalore, we faced political and quasi-political issue.
Q. All your process remains the same and your new plans?
A: Mettur was with Goodrich. We make two types of resins- PVC Suspension resins and specialty Paste -resin. We have converted the 66,000 tonnes Mettur plant to Paste PVC resin, while Cuddalore plant is making fully Suspension PVC (now making up to three lakh tonnes per annum). The technology for Cuddalore, one of the best in the world, came from Inios. We are also into other areas like Chloromethane and Polysilicons. . For Chemplast as whole, we are planning to take PVC production capacity to one million tonnes. It will take time.
But on hand, we have two ambitious projects, one for manufacture of Hydrogen Peroxide and another for production of Chlorinated PVC (CPVC). The investment in the first will be around Rs.100 crore and for the CPVC project (at Karaikal), it will come up as a joint venture with ‘Kem One SAS’, a leading European Chloro-Vinyl company, with an investment of Rs.325 crore. It will take the PVC from the Cuddalore plant. For the Hydrogen Peroxide plant at Mettur, we want to add value to the waste hydrogen that is coming out and that can be used by the textile and bleaching industry in Tirupur.
Q. The other markers that paved your path, particularly your mode of joint ventures that is touted as a model for Industry as such?
A: What we pride ourselves at Chemplast is growth with responsibility. We live up to all our commitments to all our stakeholders and constituents, whether they are our shareholders, employees, lenders or customers. We believe very strongly in the ethics of business. We have also published a code of ethics in the Group. In the last 50 years, the one thing that we take pride is in that reputation. The motto of our group says it all: Excellence with Integrity. That is mainly because of our people... We are lucky to have got some excellent people and we keep them, we take care of them.
Then is our commitment to the Environment... I took a strong commitment against pollution. We always do what is the state-of-art technology at a particular time. But (pollution control) technology changes. I said Mettur will be a ‘Zero Liquid Discharge (ZLD)’, in fact all our facilities, but we decided to start with Mettur. It was a 70-year-old plant. We decided that we would recycle and reuse the liquid. We coined the world ‘ZLD’ and it has become a lexicon and a regulation norm used by the Central Pollution Control Board (CPCB). In our marine facilities, we don’t use water from public sources. We have our RO plants both at Cuddalore and Karaikal, desalinate the seawater and use it. Then, we did another unique thing in captive power generation for a chemical industry.
In terms of corporate social responsibility, we supply water to the villages (near the Mettur plant), we run schools including one in Chennai, vocational training for women and we built the railway station at Mettur; we have been supporting tennis and cricket. As part of the golden jubilee celebrations, we are commissioning a research lab- Chemplast-Sanmar ZLD Research Lab at IIT-Madras, so that we help to improve the processes and develop new technology. We will initially put in '1.20 crore to set up the lab and it will grow further.
As far as our model of (getting into) joint venture partners, we treat our partners equally. One will keep the other comfortable. We ignore the shareholding, whoever has the majority. The shareholding pattern only decides the share of profit or dividends. But the gains for both partners will flow only through the business, no side arrangements. There is total openness in the model. Give the best to the company and get the dividends.
Chemplast was the first JV. Goodrich had 26 per cent in the company then, very unusual those days... and mid-1980s’ we have acquired 100 per cent.Two years back, we inducted Fairfax Corpn., they invested up to US dollars 300 million.
At the chemical group level, we have TCI-Egypt, it is a joint venture of sorts and we have another JV coming up, for the CVPC project with Kem One SAS of France.
Q. As Tamil Nadu moves towards total prohibition in phases, how do you look at the scenario?
A: Is it moving? (Smiles). We do not use alcohol at all now (in our processes). In any case, the allocation (of molasses from sugar mills) is done by the State government. It is not viable to use molasses anymore; it is dicey. We use imported Ethylene and make EDC... I don’t think there will be a molasses surplus situation... prices of alcohol has also gone up, so it is (alcohol route to making Ethylene) is not viable anymore.
Q. The market for PVC has grown up, but supply is short. What are the challenges for setting up local production?
A: Till ten years back, local production was 90 per cent plus of the domestic demand; the demand was growing at 10 per cent to 15 per cent. The market (for PVC resins) today is over three million tonnes, of which nearly 50 per cent is imported. Local production has not grown at all recently. Our duty structure is not conducive for manufacturers. Our duty on PVC imports is lower than many developed countries. We are the biggest sink for PVC. ... India is not doing it (adding to capacities) because it requires a lot of chlorine. An analysis is needed on the fiscal support to add to domestic manufacturing capacity, the duty structure has to be looked up...and when the world is little tightening up, incentives are required to promote local production, a little bit of protectionism even may be required... Out of the three million tonnes demand now in the country, 2.5 million tonnes goes into PVC pipes...the PVC pipes manufacturing depends on PVC;... God forbid, if there is a war and imports are stopped, our entire water supply schemes will be affected...It is the same for any basic product/commodity we rely heavily on imports. So we need a national strategy for domestic production of basic commodities;
Of course commercial needs are there, but strategically we need to build capacity (in basic commodities); That used to be the strength in India and we have lost that...Sad part is we are the largest market for many such products next to China.
The future leading markets for most commodities are India and Africa...Our per capita consumption of such commodities now is one-third of countries like Thailand and Malaysia. If we have the demand as in Thailand, Malaysia or Indonesia, at least we can come up to a standard of living of these countries. The potential demand is there.